Episodes
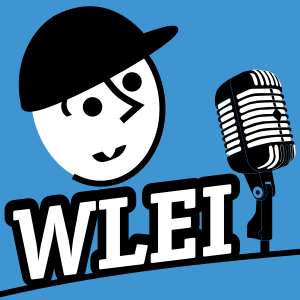
Sunday Oct 13, 2019
Sunday Oct 13, 2019
Rich Calvaruso of GE Appliances, a Haier Company, sits down with Matt Savas to talk about problem-solving. How does GE Appliances develop people through problem-solving? And how has the company's emphasis on hands-on problem-solving impacted its culture.
For more, check out our website.
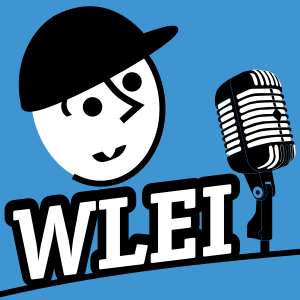
Monday Oct 07, 2019
Monday Oct 07, 2019
Dr. Lisa Yerian of the Cleveland Clinic sits down with Josh Howell, LEI President & Executive Team Leader, to talk about the spread of lean thinking at her organization. Among other things, they explore the sequence of learning between defining purpose, discovering problem-solving at the gemba, and developing lean leadership capabilities.
Additional Articles:
- Cleveland Clinic’s Prescription for Creating a Culture of Continuous Improvement
By: Lisa Yerian - How Are You Supporting Your Own Lean Transformation?
By: Lisa Yerian
- Stop Asking Your Leaders to "Support" Your Lean Transformation
By: Lisa Yerian
- Tiered Teams Solve Problems In Real Time: How a team of teams can address problems as they emerge
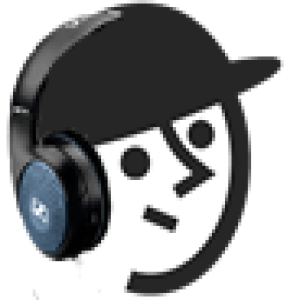
Friday Feb 08, 2019
Friday Feb 08, 2019
"If it cannot be grown, then it must be mined."
Practically everything around you exists because of mining. From phones, to computers, to cars, to glasses, to your belt buckle, they all are made from mined resources.
Laura Mottola has taken lean thinking underground, literally. Learn what lean in mining looks like, what it takes to engage those doing the work, and what is next for this ever evolving industry.
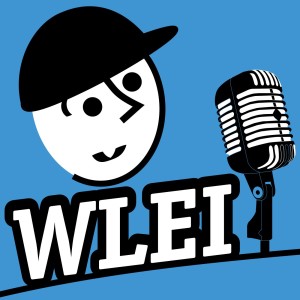
Monday Jan 21, 2019
Monday Jan 21, 2019
“It seemed nothing short of a miracle could save Ford Motor Company in the mid 2000s. Ford didn’t receive a miracle, but it did get something just as valuable: Alan Mulally.” (Daniel Miller, The Motley Fool, May 2015)
In this podcast, Alan shares:
- His view on the CEO’s role in a successful transformation.
- What “people first” leadership means to him and how his basic values and love for people guide his decision making.
- What he learned about innovation and customer focus from his lawn mowing business.
- How his early experiences with lean and Toyota shaped his views on leadership and the importance of an effective management system.
- How he has continuously improved and evolved his Working Together Management System for over 40 years, starting with aircraft development, then transformations of global organizations, and finally how it influences his work today with Google, Mayo Clinic, and Carbon 3D.
To learn more go to lean.org
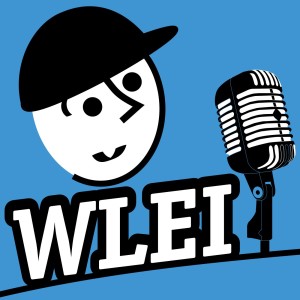
Friday Dec 21, 2018
Four Types of Problems, author Art Smalley digs in on problem solving
Friday Dec 21, 2018
Friday Dec 21, 2018
Author Art Smalley joins Chet Marchwinski to discuss problem solving and his new book Four Types of Problems from reactive trouble shooting to creative innovation.

Monday Nov 26, 2018
Monday Nov 26, 2018
In this special edition series, Designing the Future. Jim Morgan talks with Dave Pericak, the Chief Engineer of the 2015 Ford Mustang.
Pericak was featured in A Faster Horse, a documentary exploring the ins and outs of designing world's most popular sports car.
Morgan is the author of the new book, Designing the Future and has spent over 30 years in industry as a product development leader including serving as a global engineering director at Ford Motor Company during the product-led revitalization under CEO Alan Mulally.
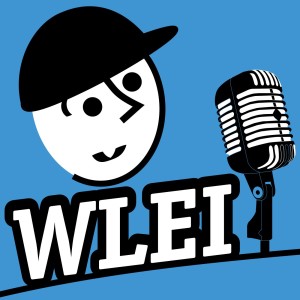
Monday Nov 05, 2018
Leadership at the Gemba with Scott Heydon and John Shook
Monday Nov 05, 2018
Monday Nov 05, 2018
Former Starbucks Executive and Senior Coach at LEI Scott Heydon, joined author and LEI Chairman John Shook for a last minute learning session at the Lean Coaching Summit.
The response was so positive we've adapted it to be a podcast.
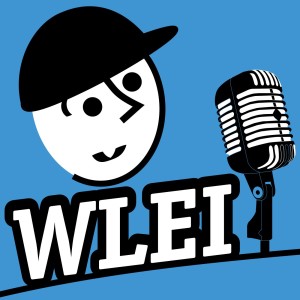
Tuesday Aug 14, 2018
Closing the Learning Gap with Steven Spear
Tuesday Aug 14, 2018
Tuesday Aug 14, 2018
Today's podcast features a conversation about closing learning gaps between LEI's CEO Eric Beuhrens and Steve Spear. Steve is author of a few works key to understanding lean. There’s “Decoding the DNA of the Toyota Producing System” and “Learning to Lead at Toyota,” both in Harvard Business Review and his book The High Velocity Edge.
As you’ll hear, Steve’s work really focuses on how Toyota as one of a few real exceptional organizations competes on the basis of a management system that optimizes on the speed, quality, and breadth of problem solving talent. He coaches these capabilities into organizations ranging from hospitals, industrial companies to the US Navy through his company HVE LLC, and teaches about them at MIT where he’s a senior lecturer.
In this conversation chapters from his book The High Velocity Edge were mentioned. To read a pdf of those chapters go to: https://www.lean.org/downloads/The-High-Velocity-Edge-Chpt-1-4and5.pdf
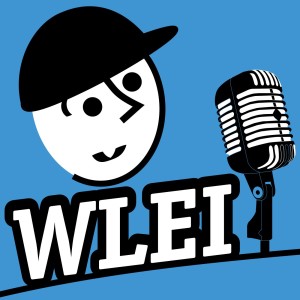
Wednesday Jul 18, 2018
Wednesday Jul 18, 2018
Can the restaurant industry change they way they've worked for decades? Legal Sea Foods has been on their lean journey for a few years and lean has influenced everything from the second that fish is caught right up until their guest has left the restaurant.
Legal Sea Foods' Executive Chef, Richard Vellante sat down with LEI's Senior Coach, Josh Howell to talk about some of the changes and experiments that have taken place at several of Legal Sea Food's locations.
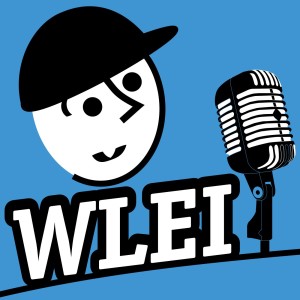
Tuesday Jun 12, 2018
Tuesday Jun 12, 2018
Two things to think about. Challenges and Culture.
Challenges shape who we are. I think we can all look at who we are and remember a few key challenges we’ve faced and how they have changed us and the way we view things. It certainly helps shape us as leaders.
Dr. Kiame Mahaniah, CEO of the Lynn Community Health Clinic.
Born in the Congo, raised in Switzerland, educated in the US, Kiame faced remarkable challenges, was immersed in multiple cultures, and has come out of all as a remarkable, yet humble leader that is focused on building consensus instead of being a top down iron fisted CEO.
Dr. Mahaniah was kind enough to sit down with LEI’s Chairman, John Shook to talk about growing up in different cultures, from the Congonese to the Quakers, and how he became a CEO in an organization trying to become lean, and helped keep that movement going. Which is something that typically ends lean’s progress in an organization.